The Art (Science) Of Pelleting
Keith C. Behnke
Kansas State University
Pelleting has been, and continues to be, a popular processing technique in feed manufacturing. In basic
terms, pelleting converts a finely ground blend of ingredients into dense, free flowing agglomerates
(pellets). There are many reasons used to justify the process, but it may be appropriate to list just a few:
- improved animal performance,
- decreased feed wastage,
- reduced selective feeding,
- improved bulk density,
- better material handling characteristics,
- destruction of deleterious organisms, and
- customer expectations.
Pelleting operations are not without cost. It is a fairly expensive process in terms of both capital and
variable costs, but the expense is usually justified in improved plant profit as well as animal performance.
The purpose of this paper is to discuss the pelleting process in terms of operations and to describe how the success or failure of the operation can impact on profits as well as animal performance.
The Process
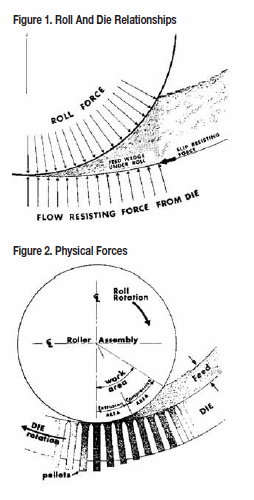
The formation of the pellet actually occurs at the "nip" between the rolls and the die. All other activities associated with the operation such as conditioning, cooling, etc. really support and augment the action at that point in the system. In order to understand the process and be in a position to make intelligent decision to improve throughput, quality or appearance, one must have a thorough understanding of what happens at the nip point. Figure 1 is a representation of the die-roll assembly and will help the reader understand the process.
Depending upon the physical characteristics of the feed, a lesser or greater proportion of the work done by the pellet mill is used for compression. For example, if the formula contains a high level of fibrous ingredients such as bagasse, bran, or ground alfalfa, the mill will expend a large amount of energy simply compressing the mash to the density of the subsequent pellet. Conversely, for a relatively dense feed such as high grain and soy meal, the mill will expend a lesser amount of energy for compression and a greater amount for throughput.
The "extrusion area" shown in the figure is the point at which the mash has reached pellet density and begins to flow through the die holes. There are many physical forces that must be dealt with in the pelleting process. Figure 2 is included to familiarize the reader with some of the major forces involved.
The primary purpose of the roll is to provide a force on the mash to densify the feed and cause it to flow toward the die. The gap between the roll and the die, the roll surface characteristics and the physical properties of the mash determine how great this potential force might be.
The die provides, not only the final diameter of the pellet, but the resistance force on the feed and has a direct influence on throughput rate and pellet quality. These two forces (roll and die) are apposite each other as shown in the diagram, but must work together to provide quality pellets at an acceptable production rate. The force generated by the roll must be greater than the resistive force provided by the die; if not, throughput is zero.
With a general understanding of the process inside the pellet chamber, it is appropriate to move to a discussion of various factors that affect both throughput and pellet quality.