Handling and Storage Of Soybeans and Soybean Meal: Part 1 - Introduction, Handling Of Soybeans And S
Ulysses A. Acasio
Department of Grain Science and Industry
Kansas State University, USA
Introduction
Soybeans represent the world’s most important oilseed as a source of vegetable oil and protein. It is grown extensively in the United States, Brazil, Argentina and China. The beans can be processed into flour for food and meal for feeds. In China, Japan and Southeast Asian countries, soybeans are used primarily in the preparation of various food products. In the U.S. and Europe, soybeans are used mainly for production of oil and meal. There are hundreds of soybean cultivars found in different parts of the world but only dozens are in commercial cultivation.
There are two kinds of soybean meal: full-fat and defatted. Both are used in the feed industry. Defatted soybean meal is a by-product of the oil extraction process and comes in either loose or pelleted form. Brazil and Argentina export their soybean meal in pelleted form while the U.S. exports soybean meal mainly in loose form.
Because of the enormous worldwide economic and nutritional importance of soybean products, it is critical to recognize the various factors contributing to the deterioration of soybeans and soybean meal. Deterioration can occur during handling and storage from harvest until reaching the end-user. The various deteriorative factors and how to minimize the effects on soybeans and soybean meal will be the main focus of the discussion below.
Handling Of Soybeans And Soybean Meal
Soybeans and soybean meal are normally handled in bulk form in developed countries, while bag handling is prevalent in developing countries. Some countries are now in a transitional period from bag to bulk handling system. Regardless of the system used, it is important to recognize the advantages and disadvantages of each system to minimize product deterioration and economic losses.
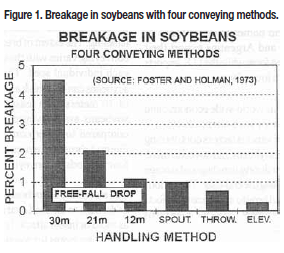
Whole Soybeans
The handling of whole soybeans involves conveying and transporting from the farm to end-user. In
the United States, it is possible for soybeans to be handled as many as 15 times from the time they
leave the farm until processing into oil and meal. This number may increase to as high as 20 for
exported material.
The structure of a soybean seed makes it susceptible to splitting and breakage during mechanical handling. The extent of breakage in soybeans during conveying varies with the impact force imposed on each individual seed. The percentage of broken soybeans can be as high as 4.5% with a free fall drop of 30 meters. The least breakage occurs when soybeans are conveyed in a bucket elevator as compared to other conveying methods studied. Figure 1 shows the extent of soybean breakage with four methods of conveying. The storability of soybeans is affected by the degree of damage to the seed coat and by other factors such as mold or insect attack. It is therefore important to inspect soybeans for mechanical and other forms of damage prior to storage. If the amount of broken or split soybeans is very high, it may be prudent to separate the broken or split grains by sieving. This material can then be used first as opposed to long-term storage with the original stock.
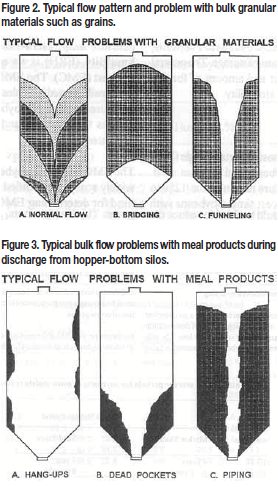
Soybean Meal
Soybean meal is difficult to handle because of poor flow ability and bridging characteristics. Soybean
meal tends to settle or consolidate over time. This phenomenon occurs in most granular materials and
becomes more severe with increased moisture, time and small particle size. Because of this, bulk
soybean meal is best stored in flat storage buildings instead of vertical silos. Standard conveyors can
be used for loading into the building and front-end loadings tractor can be used in combination with
standard conveyors for reclamation. New sweep auger designs are now available that effectively reclaim
meal products from silos. Various models and capacities are available. One model is designed to
reclaim meal products from flat- bottom silos and
another for hopper-bottom silos. However, because
of their very high initial cost, they have not become
a standard equipment yet in the industry.
Addition of calcium carbonate, calcium bentonite, or sodium bentonite at a level between 0.25% to 0.5% is effective in improving the flowability of soybean meal of the additive, and the mixing process may outweigh the potential advantage gained in improving its flowability. Other innovations such as electric vibrators and compressed air to fluidize the meal are available to improve discharge of soybean meal from storage bins.
The flow characteristics of bulk materials are dependent on individual particle shape, density, frictional property, and moisture content. For granular materials like grains, typical flow patterns during discharge from hopper bottom bins are illustrated in Figure 2. Drawing (A) shows a normal discharge pattern. The bridging and funneling problems depicted in drawings (B) and (C) occur in grains containing high content of foreign material or moisture.
Typical flow problems of meal products discharged from storage silos are shown in Figure 3. These are usually due to a combination of factors such poor hopper design, high moisture content and storage time.
Handling and Storage Of Soybeans and Soybean Meal: Part 3 - Deterioration Indicators
Handling and Storage Of Soybeans and Soybean Meal: Part 4 - Chemical Changes In Storage
Handling and Storage Of Soybeans and Soybean Meal: Part 5 - Maintenance Of Quality
Handling and Storage Of Soybeans and Soybean Meal: Part 6 - Summary